Tower-mounted crane
Much like a mobile crane, a tower-mounted crane moves loads by executing three motions: the hook is raised and lowered by means of a winch and fall, carried in a circular path by the swing gear, and carried in a radial motion by either luffing the jib or rolling a trolley carriage on its underside. The simplest of tower cranes have only these motions, but more complicated arrangements include mechanisms that allow the base to roll on a track, the crane to change elevation by climbing, or the jib to articulate on a hinge point.
In the twentieth century, tower crane and mobile-crane industries developed independently on opposite shores of the Atlantic Ocean in response to needs and cultural proclivities of their respective lands. Simply put, Europe was the realm of tower cranes, North America the realm of mobile cranes, and the rest of the world a patchwork of the two. The globalized marketplace and rapid diffusion of knowledge in the present century have eroded differences in construction practices worldwide so that the selection of a crane type now is more likely to be determined by its suitability to the work than by the country where the work is taking place. At least that is the broad picture; contractors in some localities cling longer to traditional practices than others.
Tower cranes are the lifting machines of choice worldwide for most mid- and high-rise building construction. They are used also on expansive sites where the broad hook sweep and the relative ease of coordinating multiple tower cranes is an advantage. There are niche markets for these as well; cable stay and suspension bridges, offshore oil platforms, and power plants are some examples.
In most of the world outside U.S., small tower cranes are used for modest-size residential and commercial projects. Many of these rigs are self-erecting machines that are pulled to the site by truck. In North America, similar work woulc utilize a small telescopic crane. Gradually, however, self-erecting tower cranes are penetrating the U.S. market. There is some doubt whether these machines should be classified as tower cranes; though their operating motions fit the pattern, their deployment-setup time, operation, inspection, maintenance, and demobilization-is more like that of mobile cranes.
Freestanding tower cranes range up to about 300 feet (91 m) in height; for lung lower cranes the limitation is less. Though most tower cranes free-stand and remain at a fixed height, various self-climbing arrangements permit a tower crane to attach to a building under construction and rise with it. With such supplemental means of support, a tower crane can ascend to any building height. Very high line speeds up to 1000 ft/min (5 m/s) available with some models yield good production rates even at extraordinary heights. Some machines can operate in winds up to 45 mi/h (70 km/h), which is far above mobile-crane wind limits.
Lift capability of tower cranes is gauged by a moment rating expressed as tonne-meters. The tonne-meter rating is obtained by multiplying ruled capacity in metric tons by the working radius in meters. This is done according to a method that averages a range of boom lengths and working radii. The smallest machines used for light construction have ratings of about 20 meter-tons and the very largest in production exceed this by a factor of about a hundred. Most used for heavy construction are in the range of 150 to 650 meter-tons.
The cost associated with installing and removing a tower crane is small for the self-erecting type but can be considerable for most others. At minimum, those costs would include trucking, hiring a rigging crew and an assist crane, construction of a foundation, electrical hookup, and the services of a trained technician. More complicated installations such as those which climb have considerable additional expenses. The high costs of installation, as well as the considerable investment of time and planning, make all but the smallest tower cranes a tool for longer-term projects where these expenditures can be amortized.
Excluding self-erectors, tower crane designs follow the "erector set" concept; that is, they are composed of multiple components of common design. Components connected together by pins or bolts are often interchangeable among an array of models.
As a tower is a cantilever subjected to high-bending moments that shift and reverse, each tower leg must be designed to resist alternating compressive and tensile forces. The usual stress levels and the expected number of lifetime loading cycles are not exceptional; thus leg design does not pose a difficult fatigue problem for designers. The connections between tower sections are another matter, being a perpetually nettlesome design and maintenance concern. Some designs use bolts and others use pins to join the legs of one section to the next. Bolts must be preloaded to carefully controlled levels. Failure to establish and maintain the preload can result in bolt fatigue failure. The alternative pin-type connection requires tight fabrication tolerance; imperfect towers can be either too sloppy or difficult to fit together. They also must be carefully designed to avoid the pitfall of premature fatigue failure. With the exception of a few diesel-powered machines with hydrostatic drives, tower cranes are powered by electricity and motors driving all the machinery are almost universally electric, too. The hoist motors on older machines have high- and low-speed ranges with stepped increments in each range. More recent models have variable- frequency drive or other forms of continuously adjustable speed motors with friction or eddy-current brakes and creep speed. Automatic acceleration for all motions is typical on many cranes. Remote controls are sometimes offered- A tower crane is said to be rop-.cleaving-.!erring being the preferred tower crane term for swing motion-if the swing circle is mounted near the tower top as in Figures 2.32 and 2,33 and it's said to be bollonr-slurring if the swing circle is near the base as in Figures 2.34 and 2.35. Bottom-slewing machines might have become largely obsolete had the concept not been revived by recent developments with self-erecting machines.
Relative FAQ
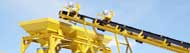
Email: sales@bossbuyer.com
Skype: bossbuyer
Market Hotline
0086-21-61435-919
Service Hotline:
0086-21-61435-919